Traffic Management For Warehousing
Traffic Management For Warehousing
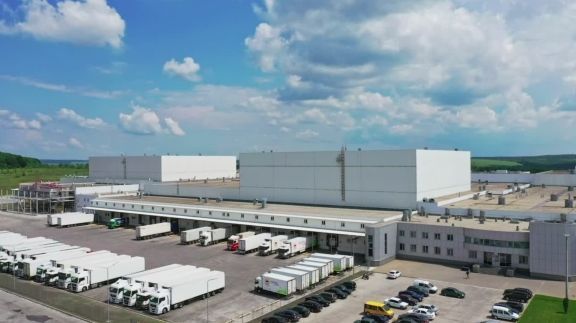
Traffic Management For Warehousing
Warehouses are typically extremely busy places and often high-pressure environments. On any given day, forklifts can be found navigating their way through complex product and rack aisles or delivering products to loading docks for delivery to trucks awaiting pickup.
Adding to the complexity, warehouse workers are often busy picking and preparing stock for customer orders, sometimes in relatively close proximity to forklifts.
Managing warehouse traffic is an important part of ensuring workplace health and safety. Vehicles, including powered mobile plants, moving in and around a workplace, reversing, loading, and unloading are frequently linked with death and injuries to workers and members of the public.
Risk Control Considerations
Let’s look at the key issues and the general risk controls for managing traffic on Warehousing Sites.
Pedestrian safety
Where there are vehicles like cars, trucks, or forklifts at your workplace there is a risk that they will collide with people. Within the warehousing site, eliminating risks to pedestrians by removing vehicles from the workplace must be considered first and the best way to protect people is to keep them physically separated from the vehicles.
Pedestrians working with vehicles including trucks and vans and powered mobile plant
The best way to protect pedestrians working with vehicles including powered mobile plant is to keep them physically separated from vehicle operating areas. Where possible workers that are not needed for the activity should be excluded from vehicle areas.
Using Loadshifting equipment
Load shifting equipment can include powered mobile plant like forklifts, ride-on pallet movers, walkie stackers and manual equipment, for example, pallet jacks and trolleys. In warehouses and factories, forklifts are commonly used to lift, stack and transfer loads. Forklifts can be one of the most high-risk pieces of equipment in the workplace and you should be aware of the risks which may include:
- Collisions with pedestrians and loads falling onto them
- Rollovers and the forklift moving unexpectedly
- Forklifts being unable to stop quickly, and
- Reduced visibility when the forklift is loaded.
The Layout of the work area
Another consideration is the layout of the workplace and the physical barriers to separate pedestrians and vehicles. These types of control measures may include:
- Minimising the cross-flow of traffic, intersections and eliminating blind spots
- Clearly defining and positioning worker and customer pick-up parking areas so they can be accessed without crossing driveways or loading dock vehicle paths
- Clearly marking pedestrian walkways or using physical barriers to separate pedestrians and powered mobile plant operating areas
- Using speed limits, stopping distances as controls where pedestrians and vehicles often interact
- Defining areas where powered mobile plant is used as ‘pedestrian exclusion zones’ and excluding powered mobile plant from pedestrian walkways and work areas; and
- Clearly indicating:
o Traffic flow with line markings or signs
o Loadshifting equipment parking areas
o Driver-designated safety zones
o Car parking areas, and
o Speed limits and speed inhibiting devices like speed humps.
Truck Loading and Unloading
Powered mobile plant, including forklifts, should not be near a driver who is attending to their vehicle whilst loading or unloading. Where drivers need to be in the loading area, for example to arrange loads, the powered mobile plant operator should not operate the plant until the driver has completed the task and is clear of the area.
Signs, warning devices and visibility
Signs - Displaying clear warning signs in areas that are easy to find and are well lit remind people of the traffic management hazards and other requirements.
Warning Devices - If there is a possibility of a powered mobile plant colliding with pedestrians, the plant should include visual warning devices like flashing lights and high-visibility markings to warn people at risk from the movement of the plant.
Visibility - Drivers should have good visibility when operating powered mobile plant and vehicles and there are several control measures that can improve visibility in the workplace.
Traffic Management Plans
Practicing traffic safety rules in the warehouse is one thing. However, unless these practices are written on paper, informal safety practices will only create confusion and risks. By creating a traffic management plan, warehouses can define safety methods that everybody – workers, visitors and contractors– must follow. Warehouse managers and supervisors can use traffic management plans as both a blueprint to train new personnel and set a benchmark to quantify points of interaction during operations.
Zenergy eLearning Program – Traffic Management for Warehousing
This online course outlines the general obligations and requirements for warehouse traffic management and control measures to prevent people being injured by moving vehicles in warehousing. The aim of this online course is to outline the duties to workers and others to ensure they are not exposed to work health and safety risks which includes implementing and reviewing control measures to prevent people being injured by moving vehicles in warehousing.
Click on the following link to review further course details: Traffic Management for Warehousing
Zenergy – Warehousing Traffic Management Plans
Zenergy experienced consultants can undertake a formal Warehousing Site Traffic Management Assessment of the site and specific areas and develop a Traffic Management Plan that manages risks and communicates information regarding control measures.
For more information on our services feel free to email us at info@zenergygroup.com.au or call 1300 333 400.