Manual Handling in the Workplace
Manual Handling in the Workplace
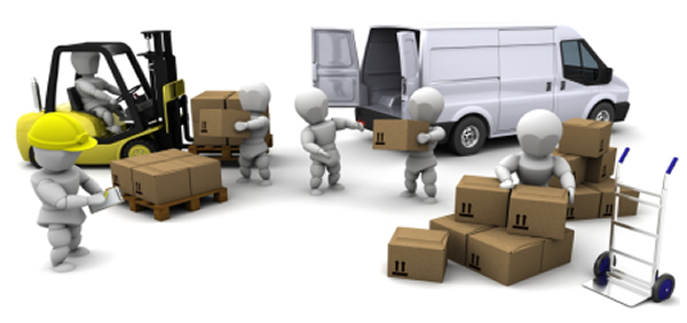
Manual Handling in the WorkplaceMost jobs involve carrying out some type of manual task using the body to move or hold an object. For many organisations, manual tasks, commonly known as manual handling, is an important part of getting the job done. Manual tasks cover a wide range of activities including stacking shelves, working on a conveyor line, repetitive tasks such as packing, assembling, cleaning, using hand-tools, operating machinery and equipment.
Injuries can occur from a number of different tasks – such as sitting for too long, doing the same task again and again, over-reaching and handling heavy items, and they can have long-term, costly impacts on your workers and your organisation.
Hazardous Manual Tasks
A manual task involves using your body to lift, lower, push, pull, carry or otherwise move, hold or restrain any person, animal or thing. Most jobs involve carrying out some type of manual tasks, but not all of them are hazardous.
In many instances, manual tasks that workers are performing would actually be classified as hazardous, known as Hazardous Manual Tasks and a manual task becomes a Hazardous Manual Task when one or more of the following risk factors are present:
- Repetitive or sustained force
- High or sudden force
- Repetitive movement
- Sustained or awkward posture
- Vibration
Musculoskeletal Disorders or MSD
These factors stress the body and can lead to a wide range of musculoskeletal disorders which are the most common workplace injuries across Australia.
Musculoskeletal Disorders or MSD, refer to an injury or disease of the musculoskeletal system. The musculoskeletal system supports and protects the body and is made up of the bones of the skeleton, muscles, cartilage, tendons, ligaments, joints and other connective tissues that supports and binds tissues and organs together.
Musculoskeletal Disorders and injuries can have long-term, costly impacts on workers and the organisation. Musculoskeletal disorders can happen slowly, through gradual wear and tear from repetitive or continuous movements, including static body positions or suddenly, through strenuous activity or unexpected movements, for example, handling a load that shifts position.
Managing The Risks
Organisations must manage the risks to health and safety relating to Musculoskeletal Disorders that are associated with hazardous manual tasks and the best way to effectively manage the risks associated with a hazardous manual task is to follow a systematic process that involves:
- identifying manual tasks that are hazardous
- if necessary, assessing the risks of injury associated with the hazardous manual task
- implementing high level risk control measures; and
- reviewing the effectiveness of control measures.
Effectiveness of Lifting Techniques Training?
Lifting technique training continues to be used as a primary way to control manual task risks in the workplace. However, the research evidence shows that providing lifting technique training on its own is not effective in minimising the risk of injury from manual tasks.
The main reason lifting technique training is not effective is because the risk factors causing the problem are not changed. Even if workers attempt to apply ‘safe lifting’ techniques, they may still be exposed to a serious injury risk.
Preventing Back Injuries - Key Things to Remember
Anytime you find yourself doing one of these things, you should think is my back at Risk?
- Heavy lifting, especially repetitive lifting over a long period of time
- Twisting at the waist while lifting or holding a heavy load
- Reaching and lifting over your head, across a table, or out the back of a truck
- Lifting or carrying objects with awkward or odd shapes
- Working in awkward, uncomfortable positions
- Sitting or standing too long in one position – sitting can be very hard on the lower back.
Zenergy eLearning Manual Handing in the Workplace
This online course introduces you to the requirements and obligations regarding manual handling and hazard manual tasks in the workplace. The aim of this online course is to give you an understanding of the hazards and risks of hazardous manual tasks how to manage the risks from hazardous manual tasks, preventing back injuries and basic lifting techniques.
Click on the following link to review further course details: Manual Handing in the Workplace
Manual Handling Risk Assessments - Contact Us to Discuss Your Needs
If you would like additional information on how Zenergy can help deliver and manage your Manual Handling Risk Assessments program which are conducted to identify the tasks in the workplace that involve hazardous manual handling, assess the risk of MSD associated with these tasks and eliminate the risk of MSD or, if this is not practicable, reduce the risk, contact us today for further information and discussion.
As industry partners to organisations around Australia we have proven experience in delivering fit for purpose practical Manual Handling solutions and professional services across a multitude of industries and sectors to meet your needs. Through a combination of our experience, academic achievements and business experience we add value to our client's business needs.
Please contact us for further information - info@zenergygroup.com.au or 1300 333 400